State Unitary Enterprise TEK SPb became the first resource supply organization in the Northern capital to launch the production of spare parts for equipment on 3D printers, the press service of Smolny told RosBalt news agency.
“The city supports enterprise initiatives for import substitution and localization. Our own production using the latest technologies gives a significant effect. Such projects reduce dependence on the supply of components that are necessary for maintenance and repair of equipment, and also increase the reliability of heat sources and heat supply systems,” Governor Alexander Beglov emphasized.
Using 3D printing, State Unitary Enterprise “TEK SPb” produces spare parts for pumping and other equipment. The new technology makes it possible to create discontinued and unavailable imported parts, replace them outside the entire set, and also avoid equipment downtime. Printing large parts takes 2 hours, medium ones – 20 minutes.
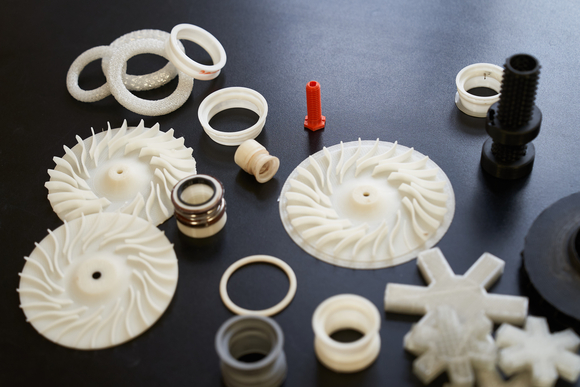
State Unitary Enterprise TEK SPb purchased two 3D printers at the beginning of 2024 – they have already paid for themselves and saved the company from problems associated with a shortage of parts. Printers operate at a speed of 600 mm/sec. With their help, specialists print mechanical seals—a company may require over 200 of these parts per year—o-rings, including for imported pumps, and mechanical components for automatic burners. Another part that the company began to produce independently is cooling impellers. The original spare part is made of a fragile material – silumin, and its failure usually required replacing the entire pump. Now you can print the part and install it on the pump – thus, 3D printers have already helped save three pieces of equipment.
“The fuel and energy complex was the first among resource supply companies in St. Petersburg to use additive technologies. This method of production is another step towards localization and import substitution. It will allow the company to save significant money, minimize the stock of parts, reduce dependence on suppliers and avoid the risks associated with unpredictable logistics. Since the developments we need, ready-made 3D models and approved production technology do not exist, our specialists are engaged in reverse engineering – creating all spare parts from scratch. The printed parts have proven their reliability in operation. This is a new practice, which we will undoubtedly scale up,” said Ivan Boltenkov, General Director of the State Unitary Enterprise “TEK SPb”.
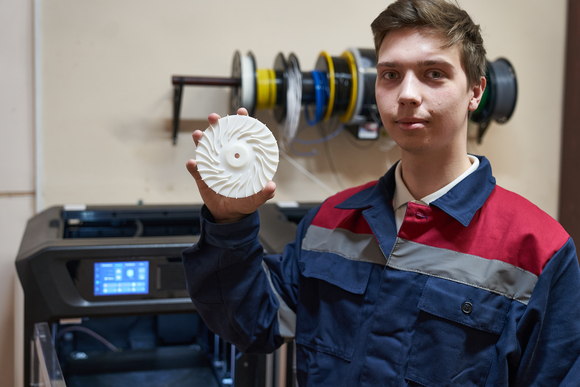
Let us recall that in 2022, one of the first domestic 3D printers, Helios, was presented in St. Petersburg, which was developed for educational projects. At the moment, this is the only such device included in the register of recommended ones by the Ministry of Industry and Trade. Nowadays the 3D printer is used in schools and in professional skills competitions. In addition, specialists from the Obukhov plant presented a more advanced model of a 3D printer – “Casket”. This is already an industrial device – its power is enough to work with nylon and durable plastic.
And in the middle of last year, the Sokol-1 3D printer was created at the St. Petersburg Prototyping Center, which prints metal parts. With its help, an exoskeleton was made that makes life easier for workers in production.
Source: Rosbalt

Mario Twitchell is an accomplished author and journalist, known for his insightful and thought-provoking writing on a wide range of topics including general and opinion. He currently works as a writer at 247 news agency, where he has established himself as a respected voice in the industry.